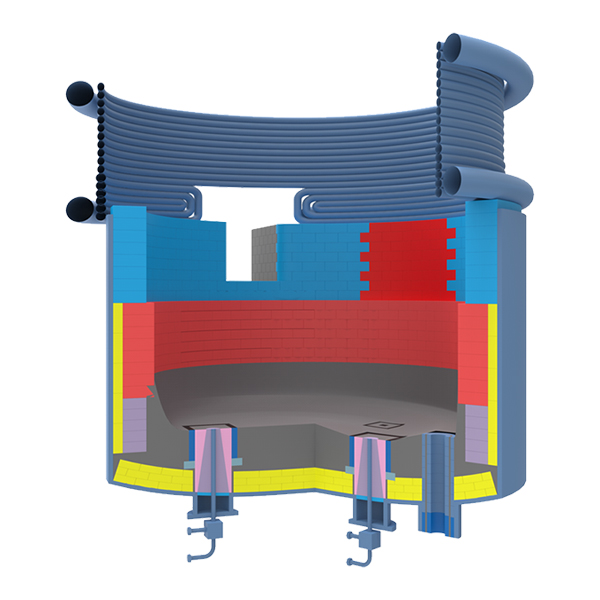
Cerințele generale pentru materialele refractare pentru cuptoarele cu arc electric sunt:
(1) Refractaritatea trebuie să fie ridicată.Temperatura arcului depășește 4000 ° C, iar temperatura de fabricare a oțelului este de 1500 ~ 1750 ° C, uneori chiar și 2000 ° C, astfel încât materialele refractare trebuie să aibă o refractaritate ridicată.
(2) Temperatura de înmuiere sub sarcină trebuie să fie ridicată.Cuptorul electric funcționează în condiții de încărcare la temperaturi ridicate, iar corpul cuptorului trebuie să reziste la eroziunea oțelului topit, astfel încât materialul refractar trebuie să aibă o temperatură ridicată de înmuiere a sarcinii.
(3) Rezistența la compresiune ar trebui să fie mare.Căptușeala cuptorului electric este afectată de impactul încărcării în timpul încărcării, de presiunea statică a oțelului topit în timpul topirii, de erodarea fluxului de oțel în timpul atingerii și de vibrațiile mecanice în timpul funcționării.Prin urmare, materialul refractar trebuie să aibă o rezistență ridicată la compresiune.
(4) Conductivitatea termică ar trebui să fie mică.Pentru a reduce pierderea de căldură a cuptorului electric și a reduce consumul de energie, materialul refractar trebuie să aibă o conductivitate termică slabă, adică coeficientul de conductivitate termică ar trebui să fie mic.
(5) Stabilitatea termică ar trebui să fie bună.În câteva minute de la atingere până la încărcare în fabricarea oțelului în cuptorul electric, temperatura scade brusc de la aproximativ 1600°C la sub 900°C, astfel încât materialele refractare sunt necesare pentru a avea o bună stabilitate termică.
(6) Rezistență puternică la coroziune.În timpul procesului de fabricare a oțelului, zgura, gazul de cuptor și oțelul topit au toate efecte puternice de eroziune chimică asupra materialelor refractare, astfel încât materialele refractare trebuie să aibă o rezistență bună la coroziune.
Alegerea materialelor refractare pentru pereții laterali
Cărămizile MgO-C sunt de obicei folosite pentru a construi pereții laterali ai cuptoarelor electrice fără pereți de răcire cu apă.Punctele fierbinți și liniile de zgură au cele mai severe condiții de funcționare.Nu numai că sunt puternic corodate și erodate de oțel topit și zgură, precum și puternic afectate mecanic atunci când se adaugă deșeuri, dar sunt și supuse radiațiilor termice din arc.Prin urmare, aceste piese sunt construite cu cărămizi MgO-C cu performanțe excelente.
Pentru pereții laterali ai cuptoarelor electrice cu pereți răciți cu apă, datorită utilizării tehnologiei de răcire cu apă, sarcina termică este crescută, iar condițiile de utilizare sunt mai stricte.Prin urmare, ar trebui selectate cărămizi MgO-C cu rezistență bună la zgură, stabilitate la șoc termic și conductivitate termică ridicată.Conținutul lor de carbon este de 10% ~ 20%.
Materiale refractare pentru pereții laterali ai cuptoarelor electrice de foarte mare putere
Pereții laterali ai cuptoarelor electrice de ultra-înaltă putere (cuptoare UHP) sunt în mare parte construiti cu cărămizi MgO-C, iar punctele fierbinți și zonele liniilor de zgură sunt construite cu cărămizi MgO-C cu performanțe excelente (cum ar fi cu matrice completă de carbon MgO-C cărămizi).Îmbunătățiți semnificativ durata de viață a acestuia.
Deși sarcina peretelui cuptorului a fost redusă datorită îmbunătățirii metodelor de operare a cuptorului electric, este încă dificil pentru materialele refractare să prelungească durata de viață a punctelor fierbinți atunci când funcționează în condiții de topire a cuptorului UHP.Prin urmare, tehnologia de răcire cu apă a fost dezvoltată și aplicată.Pentru cuptoarele electrice care folosesc robinete EBT, zona de răcire cu apă ajunge la 70%, reducând astfel foarte mult utilizarea materialelor refractare.Tehnologia modernă de răcire cu apă necesită cărămizi MgO-C cu o conductivitate termică bună.La construirea pereților laterali ai cuptorului electric se utilizează asfalt, cărămizi de magnezie lipite cu rășini și cărămizi MgO-C (conținut de carbon 5%-25%).În condiții severe de oxidare, se adaugă antioxidanți.
Pentru zonele de hotspot cel mai grav afectate de reacțiile redox, pentru construcție sunt utilizate cărămizi MgO-C cu magnezit topit cristalin mare ca materie primă, conținut de carbon mai mare de 20% și matrice completă de carbon.
Cea mai recentă dezvoltare a cărămizilor MgO-C pentru cuptoarele electrice UHP este utilizarea arderii la temperatură înaltă și apoi impregnarea cu asfalt pentru a produce așa-numitele cărămizi MgO-C impregnate cu asfalt arse.După cum se poate observa din tabelul 2, în comparație cu cărămizile neimpregnate, conținutul de carbon rezidual al cărămizilor MgO-C arse după impregnarea asfaltului și recarbonizarea crește cu aproximativ 1%, porozitatea scade cu 1%, iar rezistența și presiunea la încovoiere la temperaturi ridicate rezistența sunt Rezistența a fost îmbunătățită semnificativ, astfel încât are o durabilitate ridicată.
Materiale refractare cu magneziu pentru pereții laterali ai cuptorului electric
Căptușelile cuptorului electric sunt împărțite în alcaline și acide.Primul folosește materiale refractare alcaline (cum ar fi magnezia și materialele refractare MgO-CaO) ca căptușeală a cuptorului, în timp ce al doilea folosește cărămizi de silice, nisip de cuarț, noroi alb etc. pentru a construi căptușeala cuptorului.
Notă: Pentru materialele de căptușire a cuptorului, cuptoarele electrice alcaline folosesc materiale refractare alcaline, iar cuptoarele electrice acide folosesc materiale refractare acide.
Ora postării: Oct-12-2023